There are many factors that cause defects, and the influence of a single factor is usually caused by a combination of several factors. Therefore, the reasons should be explored from several aspects.
Contents
Hardening cracks and cracks generated after hardening
①Material.
②Shape (refers to an asymmetric geometric shape, uneven thickness, a large disparity in size, etc.). ③The temperature is uneven.
④The hardening cooling is uneven (the external and internal hardening cooling is not performed at the same time and the eccentric hardening situation).
⑤The parts that have been quenched are subjected to high-frequency hardening again.
⑥Long standing time after hardening.
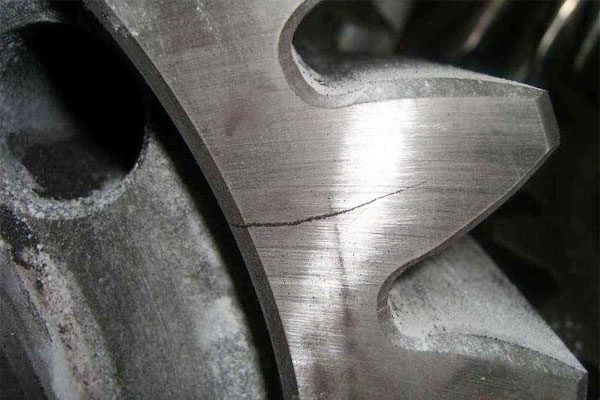
Tempering crack
①Rapid tempering Actually, the residual compressive stress has not been eliminated.
② Re-hardening occurs.

Grinding cracks
① Do not temper before grinding (use rapid tempering or partial tempering before grinding),
②Improper heat treatment systems operation before grinding (rapid tempering or partial tempering is used before grinding, and the residual tensile stress is not completely eliminated).
Overheating and melting
①Shape (thin wall, sharp corner, near hole, end, etc.)
② Heat treatment method (uneven movement up and down or left and right, slow-moving parts often occur)
③The shape of the coil.
Contact melting
①The hardening parts are deformed (due to the poor shape of the parts, or the gap between the parts and the coil is too small, or the mold supporting the parts is not suitable, etc.).
②The induction coil is deformed (due to poor coil design).
③Induction melting (the cooling water flow rate in the coil is not enough or the input power level is too large).
④ The coil is short-circuited (due to the low degree of achromatic margin).
Excessive deformation
① Uneven heat treatment.
②Uneven cooling.
③ Improper pre-heat treatment before induction hardening.
④The coil is not well-matched with the power transformer.
⑤Part shape (asymmetric shape, eccentric shape).
⑥ The hardening sequence is not suitable.
Poor deformation correction①Cold straightening (deformation occurs again in high-frequency hardening after cold straightening).
② Poor correction method.
Uneven hardness
① Uneven heat treatment.
②Uneven cooling.
③The shape of the parts is asymmetrical and the quality of each part is uneven.
④ Without pre-heat treatment, the original structure is not uniform.
Hardening range (hardening area) is not enough
①Shape (due to flange part or thick and thin connecting part).
②The shape of the coil (because the gap between the part and the coil is too large, or the copper tube of the coil is too thick).
③hardening method (because the up and down movement speed is controlled too fast during continuous hardening).
Insufficient hardness
①Material (due to low carbon content in steel, or too low carbon content in dissolved austenite during the heat treatment).
②Uneven shape (such as asymmetrical cam shape, protruding and concave parts of the gear)
③The transformation range of the layer is not suitable (due to poor control of electrical parameters, the transition layer is too thick and too thick).
The case depth of the hardened layer is not enough
①hardening method (because the up and down movement speed is too fast during continuous hardening). D heating time (because the heating duration is too short).
⑤The type, temperature, and method of the cooling medium are not suitable.
④Shape size and mass effect.
⑤Material (the choice of carbon steel is different from that of Ming Steel).
Don’t hesitate to get in touch with us, tell us your induction hardening requirements, we will give you solutions with different standards. Any of the solutions will provide benefits and disadvantages at a competitive price.