Machine tool guideways
induction hardening machine
- The key technology of heat treatment of machine tool guideways is their surface strengthening treatment.
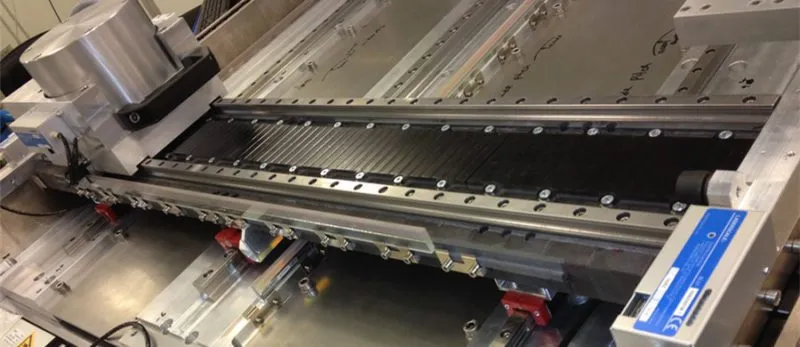
Are you looking for support or purchase information, please contact us here
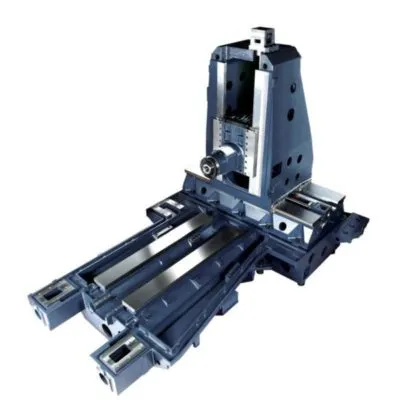
About machine tool guideways
The guideway is an important part of the machine tool. There are guideways on the machine bed, column, beam and turntable. The accuracy, machining accuracy and service life of the machine tool depend to a large extent on the geometric accuracy and intrinsic quality of the guideway, so the guideway should have the characteristics of small change, good dimensional stability and high wear resistance.
Correct and reasonable selection of machine tool guide metals and quench hardening process is one of the important measures to improve the wear resistance, scratch resistance and fatigue strength of guideways, maintain accuracy stability and prolong service life.
Heat treatment method of inlaid tool guideway:
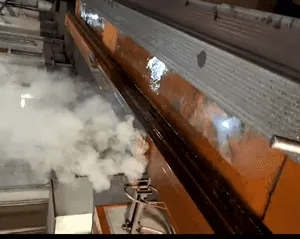
There are mainly integral quenching and tempering, carburizing quenching, surface induction quenching and nitriding treatment.
Technical conditions and heat treatment characteristics of cast iron guideways
Contact resistance quenching, flame quenching and high-temperature aging, etc. Surface quenching media mainly includes induction quenching medium, contact resistance quenching media and flame quenching media. details as follows:
- Induction hardening
- Contact resistance heating and quenching
The advantages of contact resistance heating and quenching are that the equipment and heat treatment process are simple and easy to operate. After hardened by this method, the wear resistance of ordinary gray cast iron machine tool guideways can be doubled compared with the unquenched guideways, and the scratch resistance is significantly improved. The hardness can reach 0.2-0.25mm, the hardness can reach more than 600HV, and the quenching distortion is very small. After quenching, there is no need to grind, only use the oil stone to polish the quenched pattern and it can be used.
The disadvantage is that the productivity is low, the hardened area is small, the wear resistance is lower than that of induction hardening, the hardened layer is very shallow, and it is easy to cause fire burns, so this process is mostly used for small-batch products with light guideway load or maintenance of machine tool guideways. middle.
- Flame quenching
The depth of the hardened layer obtained by flame quenching can reach 1-3mm.
However, the disadvantage is that the critical temperature is not easy to control, and it is easy to cause the phenomenon of overheating and melting. The hardness distribution is not as uniform as that of induction quenching, and the distortion of the guideway after quenching is large, which is only suitable for single-piece or small batch production. In manual operation, due to poor process stability, the temperature is difficult to control, and it has been rarely used at present.
- Laser quenching
- Induction heating equipment for machine tool guideway
- Induction quenching machine
- coil design
- Two typical examples of induction quenching of machine tool guideways
- Example 1
The cross-section of the XKA714 CNC milling machine guideway is shown in picture. The length of the guideway is 1040m, and the metal is HT300.
Heat treat technical requirements: Ultrasonic induction quenching on the upper steel alloys and inner side of the guideway, the hardness is 67-74HS.
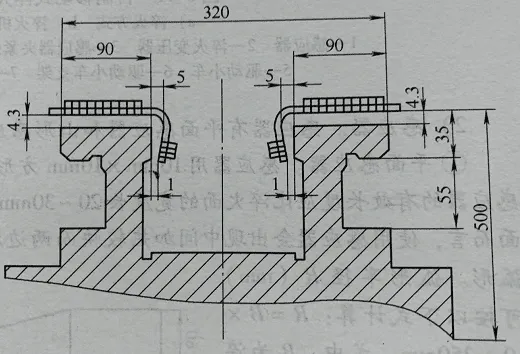
- The gap between the coil and the guideway
- Induction quenching equipment and technology
The cooling process is also important. Rapidly cooled after quenched is very necessary. The slower cooling rate sometimes will cause cracking. Rapidly cooling is needed. so the cooling rates have to be designed.the machine guide need rapidly cool down.
- Tempering
Using residual heat treating self-tempering method. The left and right guideways are quenched successively, but the direction of movement of the guideways should be the same when quenched
Towards. The maximum hardness after induction quenching is 67 ~ 74HS, and the depth of the hardened layer is > 1.5mm.
- Example 2
The metal of the CW61100E machine tool guideway is 68HS 6815 68HS 68UHT250 or HT300, and the guideway section and hardnesses requirements are as follows
As shown in the picture
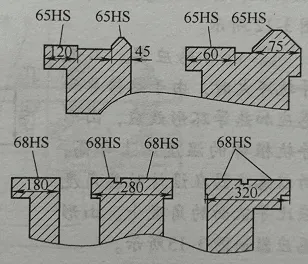
- Technical requirements before quenching Surface of guideway
The roughness reaches Ra≤3.2μm; the sharp corners must be chamfered with C2; the hardness of the guideway surface: when its length is 2500mm, the H is >190HBW; when the guideway length is >2500mm, or when the quality is >31, the H is ≥180HBW.
- Quenching equipment and process
Quenching equipment: quenching medium frequency power supply + self-made mobile Nao fire machine, as shown in the picture:
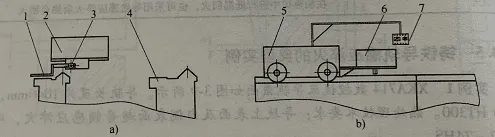
- Coil: There are two types of coils: flat coil and mountain-shaped coil.
Quenching equipment: quenching medium frequency power supply + self-made mobile Nao fire machine, as shown in the picture:
- Flat coil.
The inductor is made of 10mm x 10mm square pure low carbon steel pipe, and the wall thickness is required to be 1.5mm. The effective length of the inductor should be 20-30mm longer than the width of the quench outer side. For the guideway outer side with a quenching outer side width > 180mm, the use of the inductor will cause the phenomenon of fast heat in the middle and slow heat on both sides, so the inductor should be made into an arc. The arc radius R ( mm) can be calculated by the following formula:
R=Bx10+350mm
In the formula, B is the width of the quenched outer side (mm). Take the quenching outer side width of 180m as an example, R=180mm x 10 + 350mm =2150m, the plane coil is shown in the figure
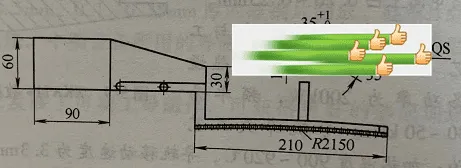
- Yamagata coil.
When the mountain-shaped guideway is quenched, the temperature of the root of the mountain-shaped guideway is higher than that of the upper part due to the annular effect such as heat conduction and induction heating.
Therefore, the angle of the coil should be smaller than the angle of the guideway surface in the design.
The coil is shown in the picture below.
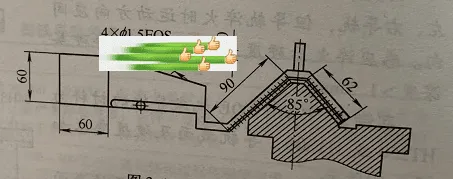
During medium frequency induction quenching, a magnetic conductor should be installed on the inductor to strengthen the magnetic field and improve the heating speed and heating temperature uniformity.
Different quenching process parameters are selected for different types of rail surfaces.
The test results are as follows: hardenss in HBW

LET US HELP
- we are dedicated to providing the best suitable induction heating solutions for our customers. Our mission starts with our free testing & solution, in which we solve the most challenging heating applications, confirming the heating process that can benefit from our systems.